PLC Based Monoblock Glass Bottle Filling Machine For Soda water / Soft Drink - DCGF
PLC Based Monoblock Glass Bottle Filling Machine For Soda water / Soft Drink For Sale, Most Competitive Price, Fast Delivery, Custom Service, Wholesale PLC Based Monoblock Glass Bottle Filling Machine For Soda water / Soft Drink, Made in China, High Quality Products!, China cheap prodocuts, china suppliers Supplier, Manufacturer.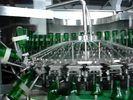
ZHANGJIAGANG Automatic Glass Bottle for Soda water/Soft drink/Beer Filling Machine/Equipment 3-in-1
?
Introduction
?
Glass bottles filling machine mono-block rinser/filler/capper is suitable for Soda water/Soft drink/Beer bottling. It can handle glass bottle and Metal crown caps, easy-open caps and Aluminum Screw Cap. DCGY series has double evacuation, 3 different rinsing media, counter-pressure filling. The speed is from 1000-24,000BPH (500 ml glass bottles)
?
?
Specifications:
?
- - - -
Application | Soda water/Soft drink/Beer |
Suitable bottle | Glass bottle |
Bottle Height | Bottle height. Φ150—φ340mm |
Bottle Diameter | Bottle dia.φ40-φ110mm |
Suitable cap type | Metal crown caps, easy-open caps and Aluminum Screw Cap |
Supply Capacity | 1,000 to 24,000 bottles per hour(500ml bottle) |
Filling style? | count-pressure filling |
Filling Temperature | Max 12 ℃ |
Voltage | 220/380V |
Automatic Grade | Automatic |
Driven Type: Electric | Electric |
Material: | High quality SUS304 stainless steel |
After-sales Service Provided | Engineers available to service machinery overseas |
- - - -
?
?
?
Description:
?
Rinsing part
1. Rotary Rinser: applicable for bottle rinsing and cleaning.
2. The new bottle is transported through the separation screw and star wheel by the clamp and turn over device; bottle neck is held upwards, after aseptic water rinsing, the bottle neck goes up and transported to another process.
3. Open design gear driving
?
Filling part
1. Imported German technology, using count-pressure filling type, achieve to fill the cleaned bottle.
2. Using mechanical valve ,fast filling with high precision filling level.
3. Using the guiding pole with cover function ;bottle held elevation design , ensures the complete seal between bottle neck and filling valve ,avoids the leakage.
4. Equip with the anti break device ;bottle break cleaning ,avoiding the next bottle .
5. Equip with complete CIP cleaning function
?
Capping part
1. Cappig part :sorted cap is capped on the filled bottle ,and then transported to the next step.
2. Capper rotates through the speed reducer machine .The cap leaves the hopper under the centrifugal function .The exit is equipped with the cap reverse device ,when the reverse cap comes ,it is changed to the right direction ;the cap quantity is controlled by the photoelectric switch ,ensures the capping falling effect.
3. If the container has the cap ,the second cap cannot go in ,which utilizes the cap .
4. And it is equipped with photo eletric swith on the slding trail ,when it tests that there is no cap ,it stops automatically
?
Competitive Advantage:
?
1, Rinsing, filling and capping can be finished on mono block machine, which reduce bottle abrasion, keeps accurate and stable driving and simple replace for bottle types.
?
2, The stainless bottle rinsing clamp with special design is durable, without contact with the bottle neck screw part, it avoids the secondary pollution.
?
3, With high filling speed and exact liquid level.
?
4, All product contact parts are made of qualified stainless steel, which wearable, stable with less malfunction.
?
5,Easy to operate and maintain.
?
6, ?PLC and transducers and other main electric parts are of world famous brands, such as OMRON, MITSUBISHI etc.
?
?
?
Benjamin machinery Company
Address: No.1 Xingyuan Road, Nanfeng Town, Zhangjiagang city, Suzhou, Jiangsu, China, 215000
Tel: 86-512-58628881
As a professional manufacture in beverage filling machinery, we have research and development, manufacture, sales and after-sale service departments. There is a group of engineers and technicians who have more than 20 years experience, committed to improvement in customer production process and deve