Thermoforming Machine: Shaping the Future of Lightweight Plastic Packaging and Components
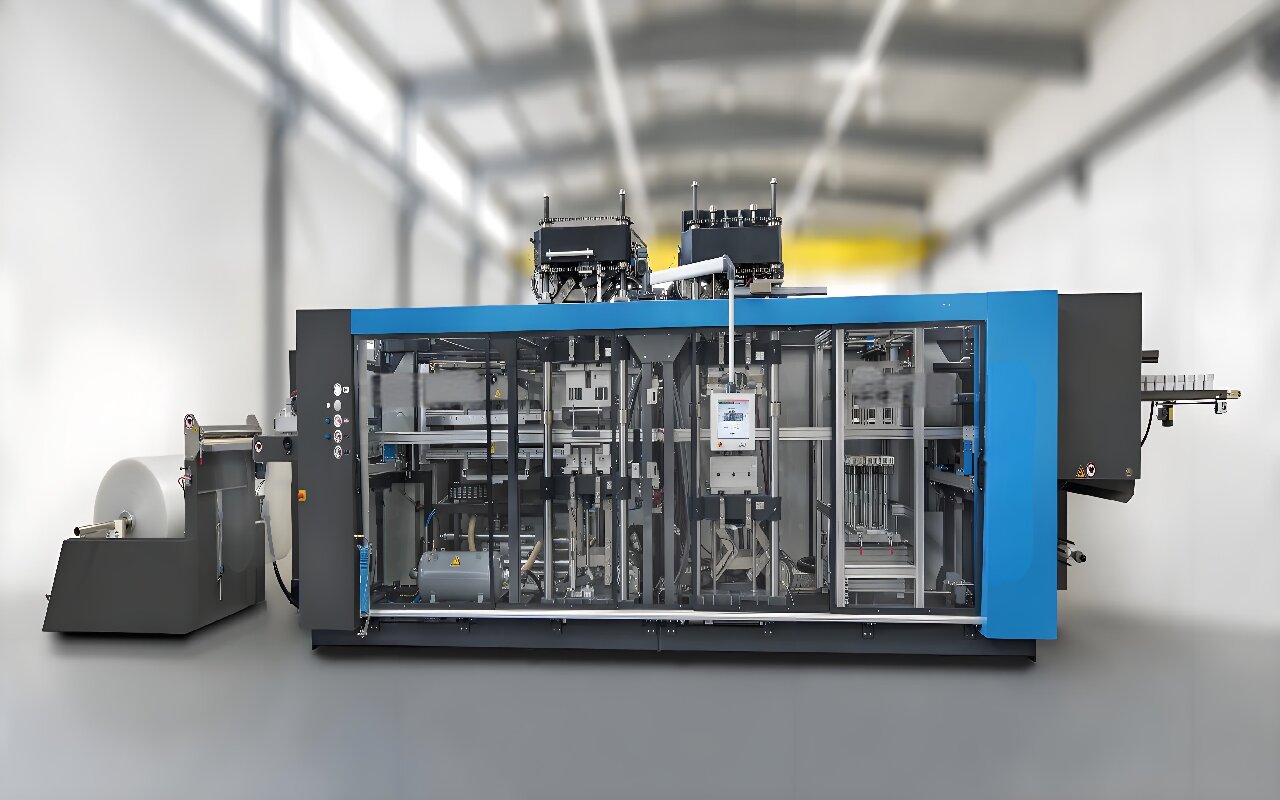
Thermoforming machines heat plastic sheets until pliable, then mold them into specific shapes using vacuum, pressure, or mechanical force. This cost-effective method dominates industries requiring lightweight, customizable, and high-volume plastic parts.
What is a Thermoforming Machine?
It comprises an oven, forming station, and trimming system. Common materials include PET, PS, and biodegradable PLA sheets.
Categories of Thermoforming Machines
- Vacuum Formers:
- Suck heated sheets onto molds using vacuum pressure. Ideal for thin-walled products (clamshells, trays).
- Pressure Formers:
- Apply compressed air to force sheets into molds for detailed designs (medical device packaging).
- Mechanical Formers:
- Use matched metal molds for high-precision parts (automotive interior panels).
- Roll-Fed Machines:
- Process continuous plastic rolls for high-speed production (yogurt cups, blister packs).
Advantages Over Other Methods
- Low Tooling Costs: Molds are 80% cheaper than injection molding counterparts.
- Rapid Prototyping: Produce samples in hours for design validation.
- Material Efficiency: Generate minimal scrap compared to CNC machining.
Primary Applications
- Food Packaging: Customizable trays, lids, and disposable cutlery.
- Medical Sector: Sterile blister packs for pills and surgical tools.
- Retail Displays: Lightweight signage and product stands.
- Aerospace: Cabin interior components made from flame-retardant ABS.
Step-by-Step Operation
- Sheet Loading: Feed pre-cut sheets or rolls into the machine.
- Heating: Warm sheets to 160–200°C until pliable.
- Forming: Apply vacuum/pressure to shape sheets over molds.
- Cooling: Solidify the formed part with fans or water mist.
- Trimming: Remove excess material using CNC routers or die cutters.
Innovations Driving the Market
- In-Mold Labeling (IML): Embed labels during forming to eliminate post-printing.
- Multi-Layer Sheets: Combine barrier layers for extended food shelf life.
- Sustainability: Bio-based PLA sheets for compostable packaging.