Plastic Rolling Machinery: Precision Calendering for High-Quality Sheets, Films, and Laminates
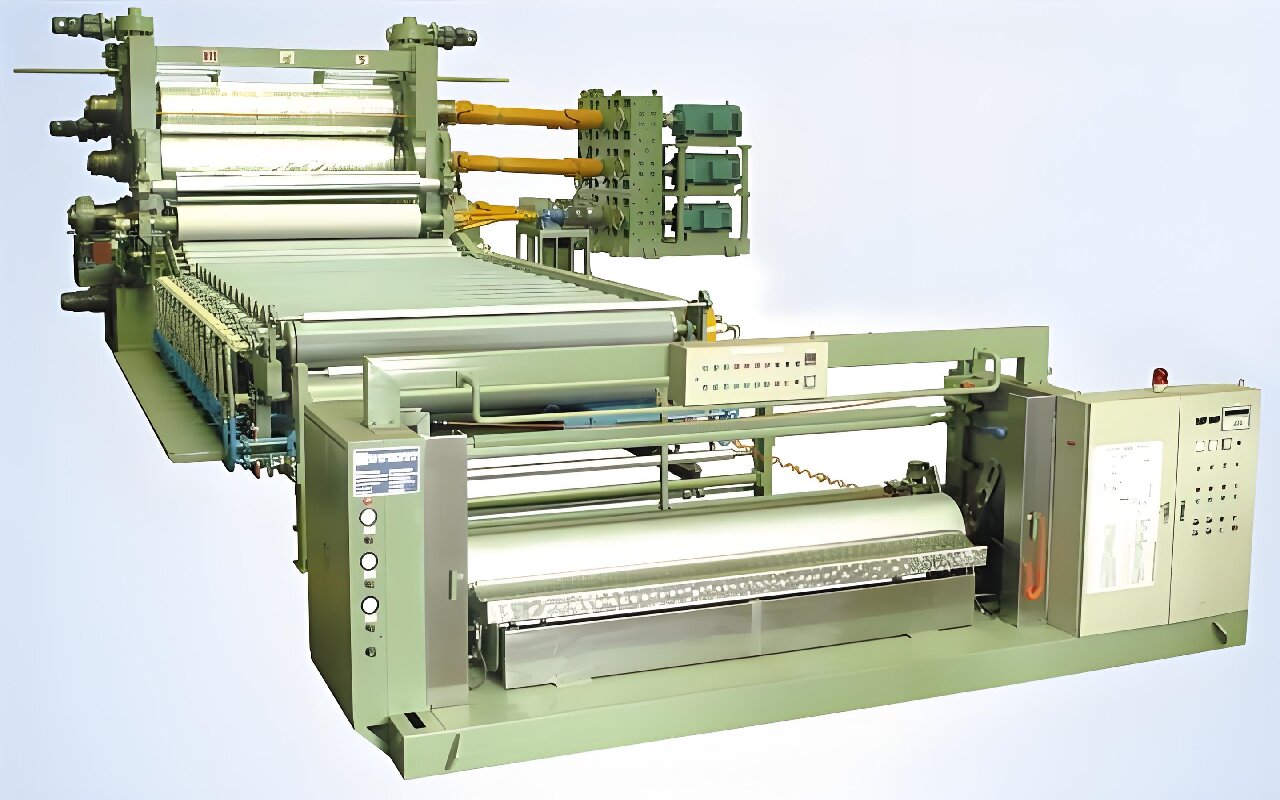
Plastic rolling machinery (calenders) processes molten polymers into uniform sheets or films by passing them through heated rollers. This method dominates industries requiring precise thickness control, such as flooring, automotive interiors, and packaging.
What is Plastic Rolling Machinery?
Calenders consist of multiple precision rollers that compress and smooth polymers into sheets of defined thickness (0.1mm to 10mm). Materials include PVC, rubber, and TPU.
Categories and Configurations
- Four-Roll Calenders:
- L-shaped rollers for flexible films (e.g., PVC cling wrap).
- Inverted-L Calenders:
- Handle rigid sheets like PVC flooring or credit cards.
- Multi-Roll Systems:
- 7–10 rollers for ultra-thin films (<0.05mm) used in medical packaging.
- Coating Calenders:
- Apply polymer layers to textiles or paper (e.g., synthetic leather).
Key Benefits
- Thickness Precision: Achieve ±0.01mm tolerance.
- High Output: Produce up to 2,000 kg/hour of film.
- Surface Finish: Glossy, matte, or embossed textures.
Industry Applications
- Construction: PVC wall panels, waterproof membranes.
- Automotive: Vinyl dashboards, acoustic damping sheets.
- Consumer Goods: Synthetic leather for furniture.
Operational Process
- Material Mixing: Blend polymer with plasticizers and stabilizers.
- Preheating: Melt compound in a Banbury mixer.
- Calendering: Feed molten polymer through rollers.
- Cooling: Solidify sheets with chilled rollers.
- Winding: Roll finished product for storage.
Sustainability Features
- Recycled Material Compatibility: Process up to 30% post-industrial PVC waste.
- Energy Recovery: Capture roller heat for preheating raw materials.