Plastic Plate Machinery: Enabling Large-Scale Production of Durable Sheets and Panels
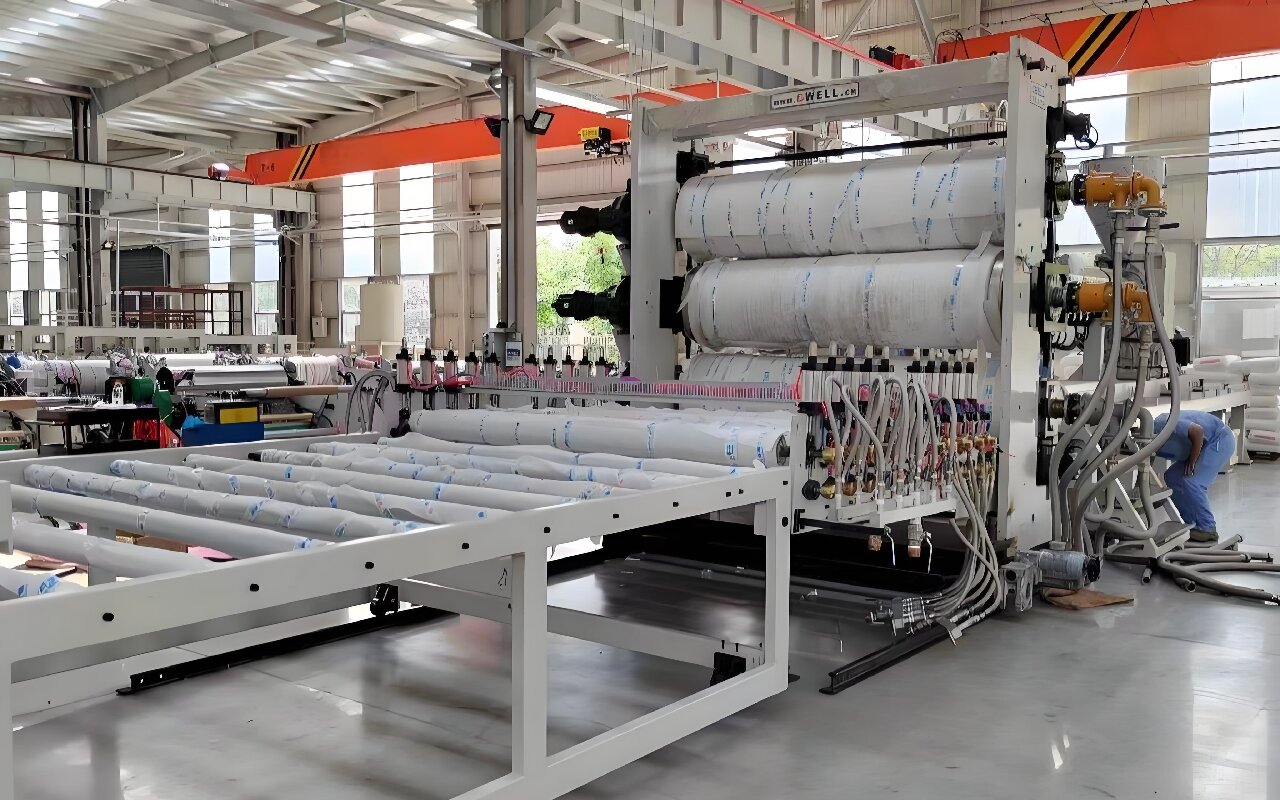
Plastic plate machinery manufactures flat sheets from materials like PVC, HDPE, and polycarbonate, which are used in construction, signage, and industrial applications. These systems prioritize precision thickness control and high throughput.
What is Plastic Plate Machinery?
It typically includes extruders, polishing stacks, and cutting systems to produce sheets ranging from 0.5mm to 50mm in thickness.
Types of Plate Production Systems
- Flat Die Extruders:
- Produce smooth sheets for thermoforming (e.g., disposable trays).
- Twin-Roll Calenders:
- Create ultra-thin films (0.1–0.5mm) for packaging.
- Multi-Layer Coextrusion Lines:
- Combine layers (e.g., ABS/PC for impact-resistant automotive panels).
- Foam Sheet Lines:
- Generate lightweight XPS boards for insulation.
Advantages Over Traditional Methods
- Thickness Precision: ±0.05mm tolerance via laser gauges.
- Material Diversity: Process engineering plastics (e.g., POM, PTFE).
- Eco-Friendly Options: Produce biodegradable PLA sheets for food packaging.
Industry Applications
- Construction: PVC wall panels, polycarbonate roofing sheets.
- Advertising: Acrylic boards for illuminated signage.
- Transportation: ABS sheets for train interior linings.
Step-by-Step Operation
- Material Feeding: Dry and blend resins with additives (UV stabilizers, flame retardants).
- Extrusion: Melt polymer through a flat die into a continuous sheet.
- Calendering: Polish sheets between heated rollers for glossy finishes.
- Cooling: Pass through chilled rolls or water baths.
- Cutting: Trim edges and slice sheets into standard sizes (e.g., 4×8 ft).
Sustainability Initiatives
- Closed-Loop Recycling: Grind offcuts and feed them back into the extruder.
- Energy Recovery: Capture waste heat to preheat raw materials.