Plastic Pipe Machinery: Engineering the Lifelines of Modern Infrastructure
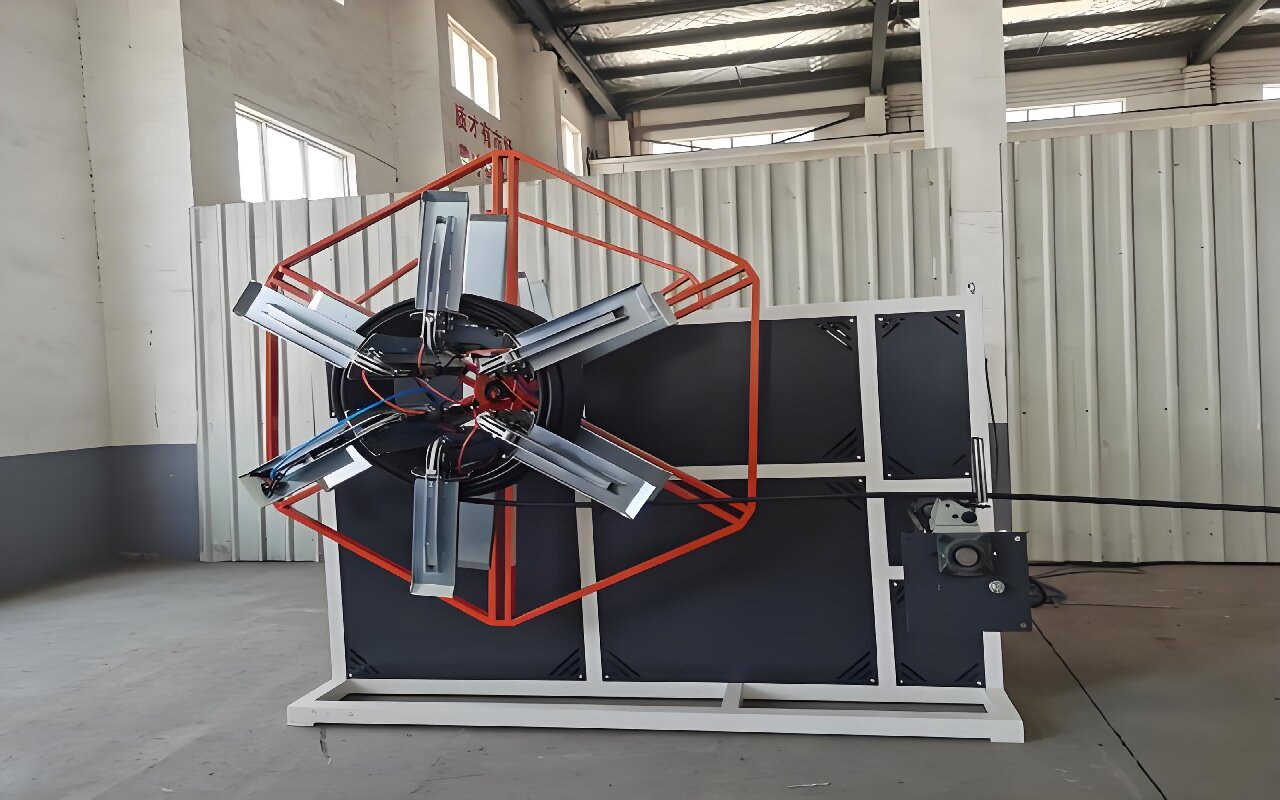
Plastic pipe machinery is the unsung hero behind the pipelines that keep cities functioning—delivering water, disposing of waste, and transporting energy. These advanced systems combine material science, automation, and precision engineering to produce pipes that withstand extreme pressures, corrosive environments, and decades of use. Here’s an in-depth look at their evolving role in global infrastructure.
Technological Breakthroughs Driving Efficiency
- Co-Extrusion Systems:
- Modern machines integrate multiple extruders to create pipes with layered structures. For example, gas pipes often have an inner layer for smooth flow, a middle layer for strength (e.g., fiberglass-reinforced HDPE), and an outer UV-resistant layer.
- Benefits: Enhanced durability, reduced leakage risks, and compliance with ISO standards for gas and chemical transport.
- Smart Cooling and Calibration:
- Laser-guided calibration units adjust pipe dimensions in real-time, compensating for material shrinkage. Closed-loop water cooling systems recycle up to 90% of water, aligning with sustainability goals.
- AI-Powered Quality Control:
- Cameras and sensors detect micro-cracks or thickness variations during extrusion, triggering automatic adjustments. This reduces waste by 15–20% compared to manual inspections.
Industry-Specific Innovations
- Water Infrastructure:
- Leak-Proof Joints: Machines now integrate socket fusion systems for seamless pipe connections, critical for aging urban water networks.
- Antimicrobial Pipes: Additives like silver ions are mixed during extrusion to prevent biofilm growth in drinking water systems.
- Oil & Gas:
- Reinforced Thermoplastic Pipes (RTP): Combining HDPE with aramid fibers, these pipes withstand 10,000 psi pressures for offshore drilling.
- Sour Gas Resistance: Modified PVC formulations prevent degradation in hydrogen sulfide-rich environments.
Sustainability and Circular Economy
- Recycled Material Integration:
- New extruders can process up to 50% post-consumer HDPE without compromising strength. Europe’s pipe manufacturers now achieve 30–40% recycled content in sewage pipes.
- Energy Recovery Systems:
- Waste heat from extruders is repurposed to preheat raw pellets, cutting energy use by 25%.
Future Outlook
- Digital Twins: Simulating pipe performance under stress to optimize designs.
- Bio-Polymers: Machinery upgrades for polylactic acid (PLA) pipes in non-pressure applications like irrigation.