Plastic Mixer: Ensuring Homogeneity and Efficiency in Polymer Processing
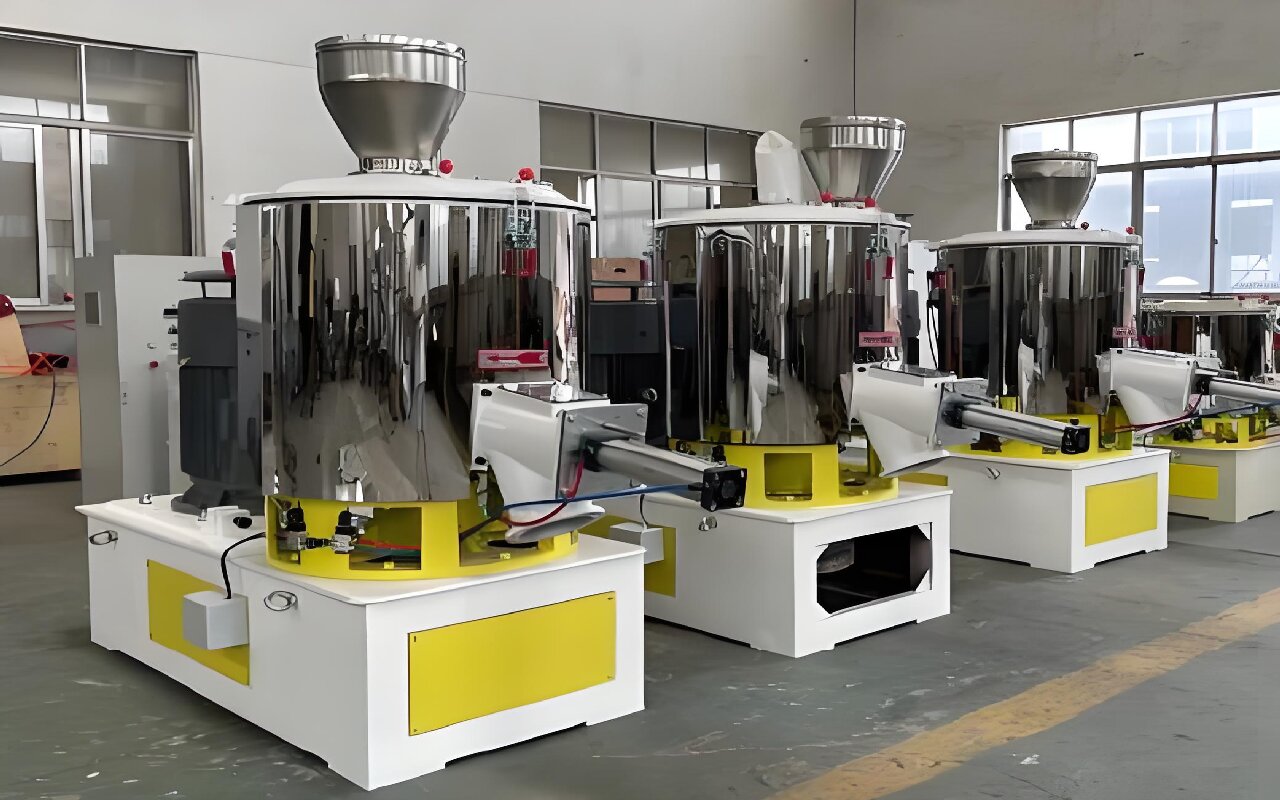
Plastic mixers blend raw polymers, additives, and recycled materials to achieve uniform composition, critical for consistent product quality in injection molding, extrusion, and compounding.
What is a Plastic Mixer?
This equipment uses mechanical agitation to combine resins, colorants, stabilizers, and fillers (e.g., glass fibers) into a homogeneous mixture.
Categories and Mechanisms
- High-Speed Mixers:
- Ribbon blades rotate at 1,000–3,000 RPM for fast blending of powders (PVC, ABS).
- Double Cone Mixers:
- Gentle tumbling action for fragile additives (e.g., flame retardants).
- Twin-Screw Mixers:
- Continuous mixing with intermeshing screws for high-viscosity materials.
- Gravimetric Blenders:
- Precision dosing via load cells for exact additive ratios (±0.5%).
Benefits
- Uniform Dispersion: Eliminate streaks or weak spots in final products.
- Energy Savings: 30% faster mixing cycles compared to manual methods.
- Scalability: Handle batches from 10kg R&D trials to 10-ton production runs.
Industry Use Cases
- Automotive: Mix carbon fiber-reinforced nylon for lightweight parts.
- Packaging: Blend recycled HDPE with virgin resin for bottles.
- 3D Printing: Prepare PLA filaments with wood or metal fillers.
Operational Guidelines
- Material Prep: Dry hygroscopic resins (e.g., PET) to <0.02% moisture.
- Loading Sequence: Add fillers first, followed by base polymer.
- Mixing Time: Optimize via torque monitoring (typically 5–15 minutes).
- Discharge: Use pneumatic systems to transfer mix to processing equipment.
Sustainability Features
- Dust Collection Systems: Capture airborne particles for reuse.
- AI-Powered Optimization: Reduce energy use by predicting ideal mixing parameters.