Plastic Machinery Parts: The Unsung Heroes Behind Efficient Polymer Processing
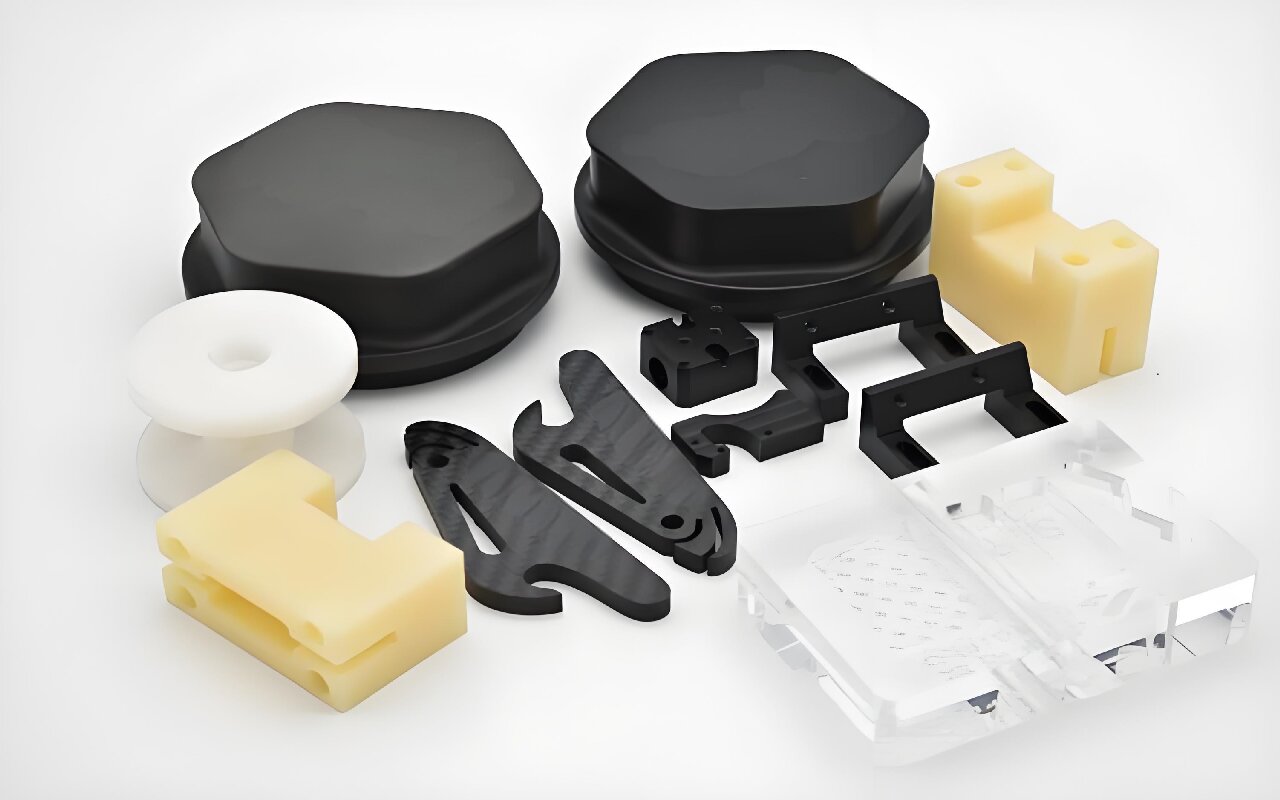
Plastic machinery parts are critical components that ensure the smooth operation of equipment like extruders, injection molders, and blow molding systems. From screws to heaters, these parts directly impact production efficiency, product quality, and machine longevity.
What Are Plastic Machinery Parts?
These include components such as barrels, screws, molds, heaters, and nozzles designed to withstand high temperatures, pressure, and wear during plastic processing.
Key Categories and Functions
- Extruder Screws and Barrels:
- Single-Flight Screws: For basic melting and mixing of polymers like LDPE.
- Barrier Screws: Enhance melt homogeneity for engineering plastics (e.g., PEEK).
- Nitrided Barrels: Resist abrasion from glass-filled materials.
- Injection Molding Nozzles:
- Open Nozzles: For low-viscosity materials like PET.
- Shut-Off Nozzles: Prevent drooling in high-pressure cycles.
- Heating Bands and Thermocouples:
- Maintain precise temperature control (±1°C) to avoid material degradation.
- Mold Inserts and Ejector Pins:
- D2 steel inserts for high-wear areas; ceramic-coated pins for smooth ejection.
Advantages of Premium Parts
- Extended Lifespan: Hardened screws last 3–5x longer than standard models.
- Energy Efficiency: Optimized screw designs reduce power consumption by 15%.
- Consistency: Precision-machined parts minimize product defects like warping.
Applications Across Industries
- Automotive: High-strength molds for dashboards and bumpers.
- Medical: Corrosion-resistant barrels for implant-grade PEEK processing.
- Packaging: Wear-resistant screws for recycled HDPE film production.
Maintenance and Operation Tips
- Daily Checks: Inspect screws for wear or material buildup.
- Lubrication: Apply high-temperature grease to screw threads weekly.
- Calibration: Use infrared thermometers to verify heater accuracy monthly.
- Storage: Keep spare molds in dehumidified rooms to prevent rust.