Plastic Loader: Automating Material Handling for Efficient Production Lines
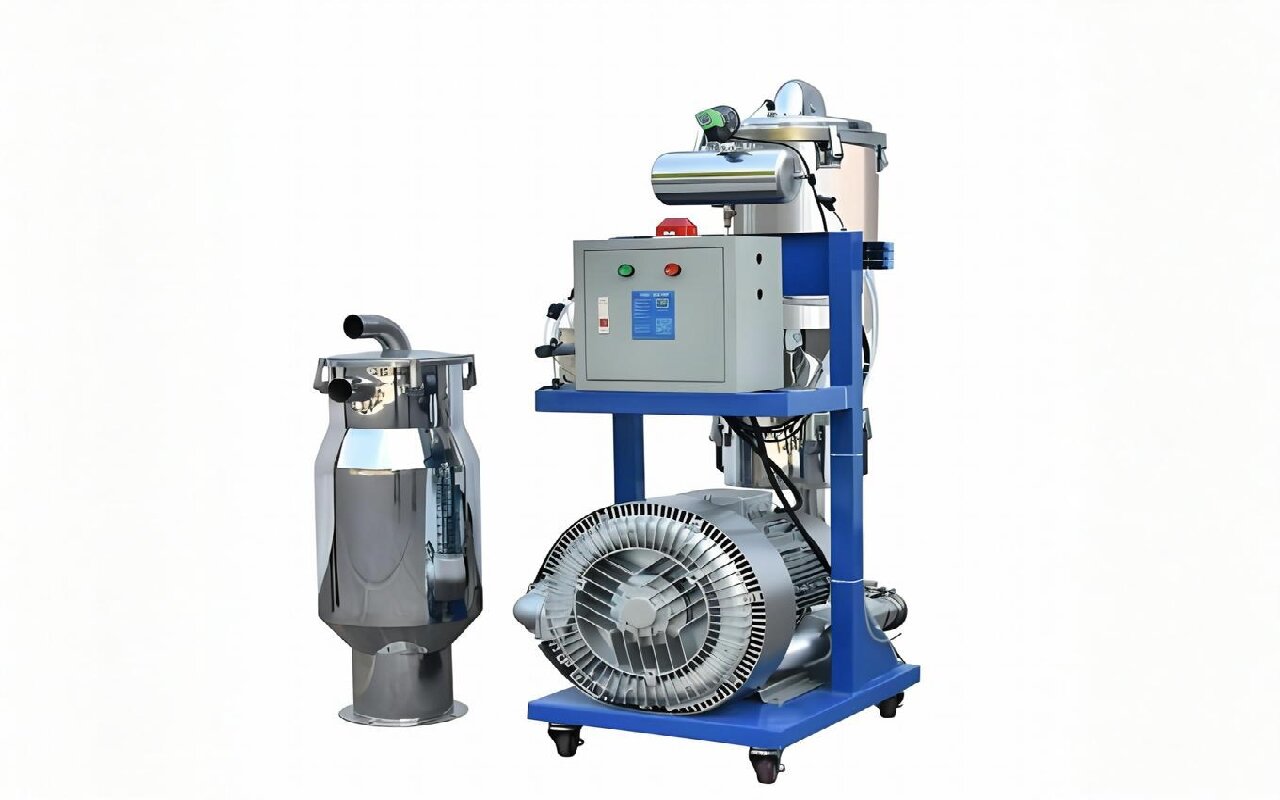
Plastic loaders (also known as material loaders or conveyors) automate the transfer of plastic pellets, powders, or regrind from storage to processing equipment like extruders and injection molders. These systems minimize manual labor and ensure consistent material flow.
What is a Plastic Loader?
It uses vacuum pumps, hoses, and sensors to transport raw materials from silos or containers to hoppers. Advanced models integrate with IoT for real-time inventory tracking.
Types of Plastic Loaders
- Central Loaders:
- Serve multiple machines via a network of pipes. Ideal for large factories.
- Portable Loaders:
- Mobile units for small-batch or R&D facilities.
- Vacuum Loaders:
- Use negative pressure to move materials without contamination.
- Gravimetric Loaders:
- Precisely weigh materials for blending accuracy (±0.1%).
Benefits
- Labor Reduction: Eliminate manual scooping and lifting.
- Contamination Control: Closed systems prevent dust and moisture ingress.
- 24/7 Operation: Uninterrupted material supply for continuous production.
Applications
- Injection Molding: Feed hoppers with ABS, PC, or nylon pellets.
- Blow Molding: Transport HDPE for bottle production.
- Compounding: Load additives like colorants or flame retardants.
Operational Guidelines
- Setup: Connect hoses to material source and destination hopper.
- Calibration: Adjust suction power based on material density (e.g., PP vs. PVC).
- Monitoring: Use control panels to track material levels and detect blockages.
Innovations
- AI-Powered Predictive Maintenance: Alert operators to filter replacements or hose wear.
- Energy-Efficient Motors: Reduce power consumption by 40%.