Plastic Extruder: Transforming Raw Materials into Versatile Plastic Products
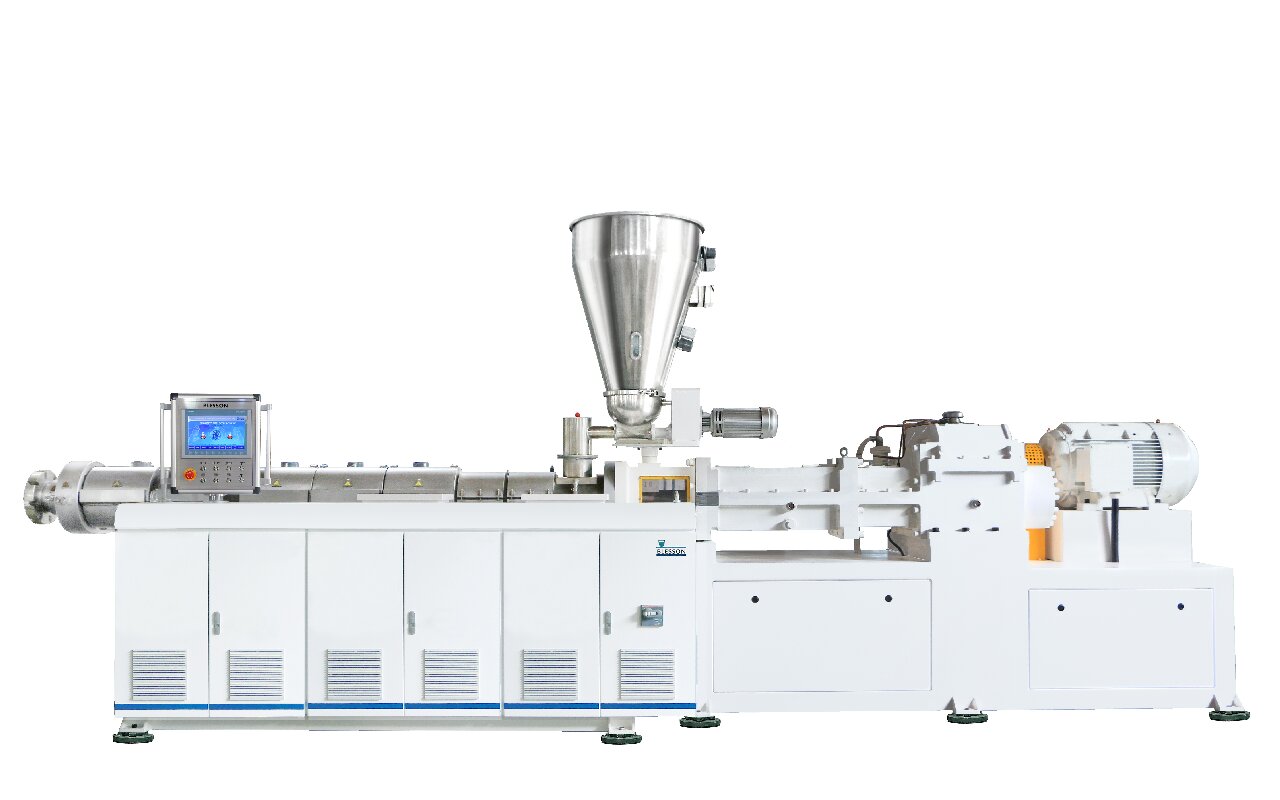
A plastic extruder is a machine used to shape raw plastic materials into continuous profiles, such as pipes, sheets, films, and filaments. It is a key piece of equipment in the plastic manufacturing industry, enabling the production of a wide range of products. This article explains what a plastic extruder is, its types, functions, benefits, and additional applications.
What is a Plastic Extruder?
A plastic extruder is a device that melts raw plastic pellets or granules and forces the molten material through a die to create a specific shape. The process involves heating, mixing, and shaping the plastic, which is then cooled and cut to the desired length.
Types of Plastic Extruders
- Single-Screw Extruders:
- Use a single rotating screw to melt and push plastic through the die, ideal for simple profiles.
- Twin-Screw Extruders:
- Feature two intermeshing screws for better mixing and handling of complex materials.
- Co-Extruders:
- Combine multiple layers of plastic to create products with enhanced properties.
- Blown Film Extruders:
- Produce plastic films by inflating molten plastic into a bubble.
- Sheet Extruders:
- Create flat plastic sheets for packaging or construction.
Functions and Benefits
- Versatility:
- Can produce a wide range of plastic products, from pipes to films.
- Efficiency:
- Continuous production process reduces waste and increases output.
- Cost-Effectiveness:
- Lowers production costs by automating the shaping process.
- Customization:
- Allows for precise control over product dimensions and properties.
- Sustainability:
- Can process recycled plastics, reducing environmental impact.
Applications
- Plastic Pipe Manufacturing:
- Produce pipes for plumbing, irrigation, and construction.
- Packaging:
- Create plastic films, bags, and containers.
- 3D Printing:
- Extrude plastic filaments for additive manufacturing.
- Automotive Industry:
- Manufacture plastic components like dashboards and bumpers.
- Construction:
- Produce plastic sheets, profiles, and insulation materials.
Key Advantages Over Traditional Methods
- Precision:
- Ensures consistent product dimensions and quality.
- Speed:
- Faster production compared to manual shaping methods.
- Material Efficiency:
- Minimizes waste by recycling excess plastic.
Operation Steps
- Feeding:
- Load raw plastic pellets or granules into the extruder hopper.
- Melting and Mixing:
- Heat and mix the plastic in the extruder barrel.
- Extrusion:
- Force the molten plastic through a die to shape it.
- Cooling and Cutting:
- Cool the extruded product and cut it to the desired length.
Maintenance Tips
- Clean the extruder barrel and screw regularly to prevent residue buildup.
- Inspect and replace worn parts (e.g., screws, dies).
- Lubricate moving components to ensure smooth operation.
Conclusion
Plastic extruders are essential for modern plastic manufacturing, offering versatility, efficiency, and cost savings. By automating the shaping process, these machines enable the production of high-quality plastic products for various industries. Whether for packaging, construction, or automotive applications, investing in a plastic extruder ensures consistent and sustainable production.