Plastic Drying Machine: Eliminating Moisture for Superior Polymer Processing and Product Quality
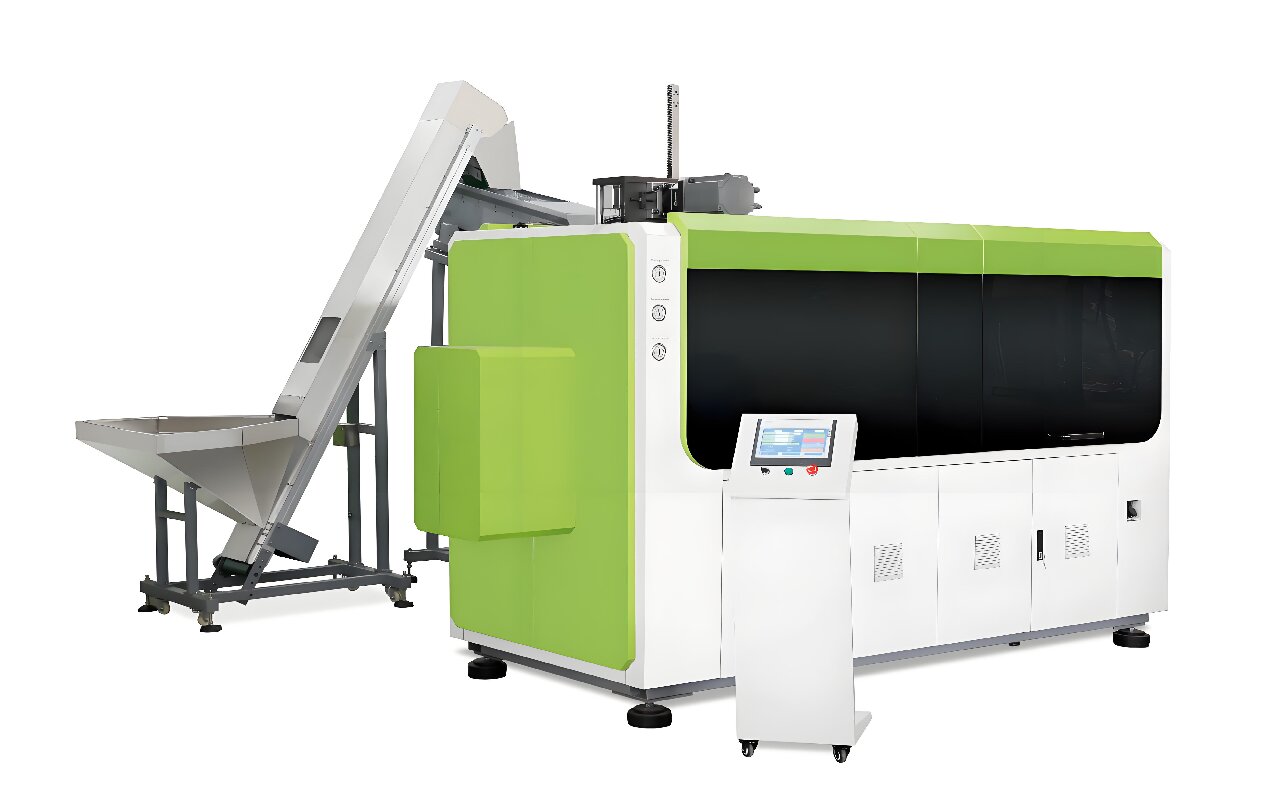
Plastic drying machines are essential for removing moisture from hygroscopic resins like PET, nylon, and ABS, ensuring optimal melt flow and preventing defects such as bubbles, splay marks, or weakened mechanical properties.
What is a Plastic Drying Machine?
These systems use heat, airflow, or desiccants to reduce moisture content in plastic pellets to as low as 0.005% before processing. Common types include hopper dryers, dehumidifying dryers, and vacuum dryers.
Types of Plastic Drying Systems
- Hopper Dryers:
- Integrated with processing machines (e.g., injection molders) for continuous drying.
- Ideal for small batches of materials like PC or PMMA.
- Dehumidifying Dryers:
- Use desiccant wheels to absorb moisture from airflow.
- Critical for PET and PLA in food packaging.
- Vacuum Dryers:
- Remove moisture under low pressure for heat-sensitive resins (e.g., TPU).
- Portable Dryers:
- Compact units for R&D labs or job shops.
Key Advantages
- Defect Prevention: Eliminate voids and surface imperfections.
- Energy Efficiency: Recirculate hot air to cut energy use by 40%.
- Versatility: Handle pellets, powders, and regrind.
Applications
- Automotive: Dry nylon for engine components.
- Medical: Ensure moisture-free PEEK for surgical tools.
- Packaging: Process rPET for beverage bottles.
Operation Steps
- Loading: Fill pellets into the dryer hopper.
- Drying Cycle: Set temperature (80–180°C) and time (2–4 hours).
- Moisture Monitoring: Use hygrometers to confirm dryness.
- Feeding: Transfer dried material to processing equipment.
Innovations
- IoT Integration: Track drying parameters via mobile apps.
- Dual-Stage Drying: Combine desiccant and hot air for ultra-dry resins.