Injection Molding Machine: Precision Manufacturing for Plastic Products
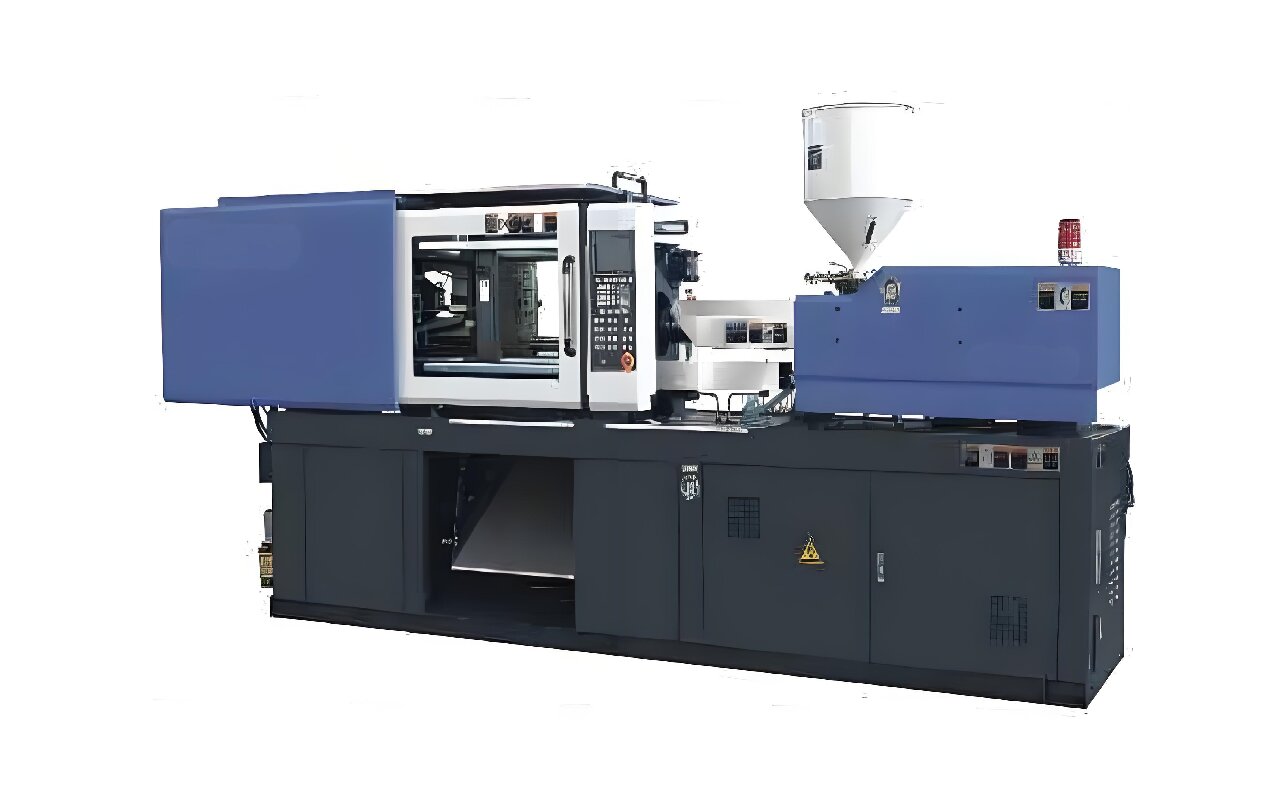
An injection molding machine is a device used to produce plastic parts by injecting molten plastic into a mold. It is widely used in industries like automotive, electronics, and consumer goods for mass-producing high-precision components. This article explains what an injection molding machine is, its types, functions, benefits, and applications.
What is an Injection Molding Machine?
An injection molding machine melts plastic pellets and injects the molten material into a mold to create shaped parts. The machine consists of a clamping unit, injection unit, and control system to ensure precise production.
Types of Injection Molding Machines
- Hydraulic Machines:
- Use hydraulic systems for clamping and injection, suitable for large parts.
- Electric Machines:
- Energy-efficient and precise, ideal for small, complex parts.
- Hybrid Machines:
- Combine hydraulic and electric systems for balanced performance.
- Vertical Machines:
- Designed for insert molding or overmolding applications.
Functions and Benefits
- High Precision:
- Produces parts with tight tolerances and complex geometries.
- Mass Production:
- Enables rapid manufacturing of identical parts.
- Material Efficiency:
- Minimizes waste by reusing excess plastic.
- Versatility:
- Works with thermoplastics, thermosets, and elastomers.
- Cost-Effective:
- Lowers per-unit costs for large production runs.
Applications
- Automotive:
- Produce dashboards, bumpers, and interior components.
- Electronics:
- Manufacture casings, connectors, and circuit boards.
- Medical Devices:
- Create sterile, high-precision components.
- Consumer Goods:
- Make toys, kitchenware, and packaging.
Key Advantages Over Traditional Methods
- Speed:
- Faster production compared to manual molding.
- Consistency:
- Ensures uniform quality across all parts.
- Automation:
- Reduces labor costs and human error.
Operation Steps
- Clamping:
- Secure the mold in the machine.
- Injection:
- Melt and inject plastic into the mold cavity.
- Cooling:
- Allow the part to solidify.
- Ejection:
- Remove the finished part from the mold.
Maintenance Tips
- Clean molds and screws regularly.
- Inspect hydraulic systems for leaks.
- Lubricate moving parts to prevent wear.
Conclusion
Injection molding machines are vital for modern manufacturing, offering precision, efficiency, and scalability. By automating the production of plastic parts, these machines support industries ranging from automotive to healthcare.