Blow Molding Machine: Crafting Hollow Plastic Products with Efficiency
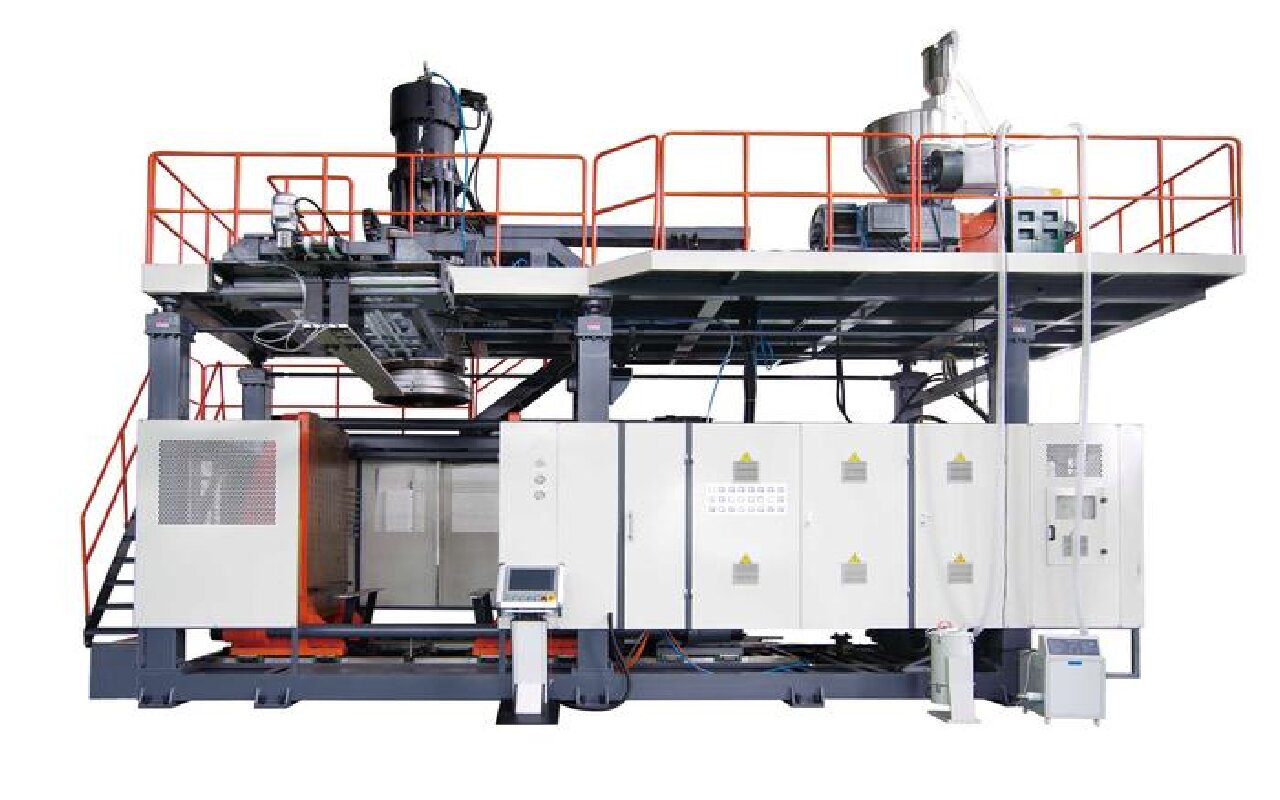
A blow molding machine is a device used to create hollow plastic products like bottles, containers, and tanks by inflating molten plastic into a mold. It is essential in packaging, automotive, and industrial manufacturing. This article explains what a blow molding machine is, its types, functions, benefits, and applications.
What is a Blow Molding Machine?
A blow molding machine heats plastic into a parison (hollow tube), places it in a mold, and inflates it with air to form the desired shape. The process is ideal for lightweight, durable containers.
Types of Blow Molding Machines
- Extrusion Blow Molding:
- Extrudes a parison and inflates it into a mold; used for bottles and drums.
- Injection Blow Molding:
- Combines injection molding and blow molding for high-precision medical or cosmetic bottles.
- Stretch Blow Molding:
- Stretches and inflates preforms (e.g., PET bottles) for enhanced strength.
- Rotational Blow Molding:
- Rotates molds to create large, complex shapes like fuel tanks.
Functions and Benefits
- Lightweight Design:
- Produces durable, thin-walled containers.
- Cost-Effective:
- Low material waste and high production speed.
- Versatility:
- Creates bottles, tanks, and automotive parts.
- High Volume Production:
- Suitable for mass manufacturing.
- Material Flexibility:
- Works with HDPE, PET, PVC, and other plastics.
Applications
- Packaging:
- Produce bottles for beverages, chemicals, and cosmetics.
- Automotive:
- Manufacture fuel tanks, air ducts, and fluid containers.
- Industrial:
- Create storage drums and chemical tanks.
- Consumer Goods:
- Make household containers and toys.
Key Advantages Over Traditional Methods
- Speed:
- Faster than manual or glass-based production.
- Uniformity:
- Ensures consistent product quality.
- Scalability:
- Adaptable to small or large production runs.
Operation Steps
- Parison Formation:
- Extrude or inject a hollow plastic tube.
- Mold Clamping:
- Secure the mold around the parison.
- Inflation:
- Blow air to expand the parison into the mold shape.
- Cooling and Ejection:
- Cool the product and remove it from the mold.
Maintenance Tips
- Clean molds and air nozzles regularly.
- Inspect heating elements for efficiency.
- Lubricate mechanical parts to prevent wear.
Conclusion
Blow molding machines are vital for producing hollow plastic products efficiently and cost-effectively. From packaging to automotive parts, these machines enable high-quality, large-scale production.