16mm Plate Strip Billet Alloy Copper Continuous Slab Caster Double Strand - BSC
16mm Plate Strip Billet Alloy Copper Continuous Slab Caster Double Strand For Sale, Most Competitive Price, Fast Delivery, Custom Service, Wholesale 16mm Plate Strip Billet Alloy Copper Continuous Slab Caster Double Strand, Made in China, High Quality Products!, China cheap prodocuts, china suppliers Supplier, Manufacturer.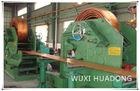
?
16mm Plate Strip Billet Alloy Copper Continuous Slab Caster Double Strand?
?
?
Ⅰ .Major Technical Parameters of Equipment:
?
- - - -
1 | Smelting furnace: |
1.1 | Total capacity of furnace | 5.0T |
1.2 | Effective capacity of furnace | 2.5T |
1.3 | Furnace voltage | 380V |
1.4 | Furnace power | 600KW |
1.5 | Melting rate | 2t/h |
1.6 | Power factor after compensation: | 0.95-1.0 |
1.7 | Number of phases and connection mode of inductor: | Single-phase series-connection ? |
1.8 | Rated capacity of transformer: | 900KVA water-cooled autotransformer (380V incoming-line, three-phase, ? ? |
1.9 | coil cooling mode: | Water-cooling |
1.10 | Cooling water consumption: | 5m3/h |
1.11 | Maximum temperature of furnace: | 1500℃ |
2 | Holding furnace section | ? ? |
2.1 | Effective capacity of furnace: | 4.0T |
2.2 | Effective casting capacity: | Less than 85 dB |
2.3 | Rated voltage: | 380V |
2.4 | Rated power : | 250KW |
2.5 | Rated capacity of transformer: | 400KVA water-cooled autotransformer (380V incoming-line, three-phase, no-load stepped voltage-regulating). |
2.6 | Power factor after compensation: | 0.95-1.0 |
2.7 | Temperature control precision: | ±8℃ |
2.8 | Maximum temperature of furnace: | 1300℃ |
2.9 | Coil cooling mode: | Water-cooling ? |
3 | Mould | ? |
3.1 | width | 380- 500mm |
3.2 | thickness | 16-20mm. |
3.3 | Material | 1Cr18Ni9Ti stainless steel, lined with copper bush (made of T2 copper) |
4 | Secondary cooling device | ? |
4.1 | Water consumption: | 3m 3/h |
4.2 | Water pressure: | 0.2-0.3Mpa |
5 | Withdrawal machine | ? |
5.1 | Maximum pushing and drawing force: | 50KN |
5.2 | Speed: | Speed: |
5.3 | Minimum stroke range: | 0.1mm ? |
5.4 | Shortest standby time | 0.01S |
5.5 | AC servo motor: | Siemens motor (11KW) |
5.6 | Rated rotation speed of motor: | 3000r/min |
5.7 | Static torque: | △Tw= 60K Mo (at 60) 70N-M |
6 | Double-billet hydraulic upper shearing machine: ? |
6.1 | Shearing force: | 600KN |
6.2 | shearing thickness: | 20mm |
6.3 | Shearing width: | 500mm |
6.4 | Shearing speed: | 0- 5mm/s ? |
6.5 | Shearing stroke: | 80mm |
6.6 | Maximum follow-up stroke of shearing machine: | 200mm |
7 | Coiler machine unit | ? |
7.1 | Power: | 5.5KW |
7.2 | Rotational speed: | 1420r/min |
7.3 | Coiler displacement stroke: | 800mm |
8 | Hydraulic station | ? |
8.1 | Motor power of hydraulic station for smelting furnace and holding furnace: ? | 2× 7.5KW |
8.2 | Motor power of hydraulic station for withdrawal machine: | 2× 7.5KW |
8.3 | Motor power of hydraulic pump for upper shearing machine: | 2× 11KW ? |
8.4 | Motor power of hydraulic pump for coiler: | 2× 7.5KW |
- - - -
?
Ⅱ. Specifications:
1. Types of casting specifications
* Production variety: copper base alloy (white brass) billet coils
?
2.?Specification of finished-product coil
? 2.1 Number of billets: 2 strips
? 2.2 Billet width: 380mm-500mm
? 2.3 Billet thickness: 16- 20mm
? 2.4 Inside diameter of coil: minimum Φ 600- 800mm
? 2.5 Outside diameter of coil: maximum Φ1800mm
? 2.6 ?Maximum weight of coil: max: 6000kg
?
3. Guarantee value of billet thickness difference
? 3.1 Transverse thickness difference of billet: <0.75mm—0.3 (After mould modification)
??3.2?Longitudinal thickness difference of billet: <0.3mm (After mould modification)
? 3.3 Average energy consumption for smelting by smelting furnace: 250-380kwh/t
??3.4 Average energy consumption for temperature preservation by holding furnace: 50-80kwh/t
??3.5 Maximum pushing and drawing force: 50KN
? 3.6?Pushing and drawing speed range: 1.5-70mm/ sec
? 3.7?Average maximum casting speed: 300mm/ min
? 3.8 Maximum shearing force of hydraulic shear: 600KN
? 3.9?Coiling speed of coiler: 750mm/min
?
Ⅲ.Process:?
? ? ?Burdening (Returns should be baled) → Smelting furnace → Chemical analysis → Heating up the sealed launder → Crystallizer → Primary cooling → Secondary cooling → Withdrawal machine → Shearing machine →Coiler
? ??Select the raw materials according to process document, determine the feeding procedure according to melting points of metallic elements, furnace burden proportions, and difficulty of oxidation burning losses, and charge the raw material into the smelting furnace; When smelting, add certain thickness of covering agent into the furnace, which shall be supplemented in-time; When the molten copper inside the furnace reaches tapping temperature, lab-test the composition of molten copper inside the furnace; Before tapping, completely clean out the clinkers in molten copper; After the tapping of each furnace, keep around 800 kg molten copper inside the furnace, as the starting block. Transfer the molten copper (molten and well-adjusted in the melting chamber) through the sealed launder into the holding furnace, control the temperature of molten copper, keep the molten copper inside the holding furnace at the casting temperature and at certain level range. Under the action of level, the molten copper flows into the crystallizer, and get crystallized into plate-type copper billet through primary cooling by crystallizer. Under the continuous drawing by withdrawal machine, the plate billet of required shape is formed. Secondary cooling system is installed at plate billet outlet, and the flow rate of cooling water is adjustable. The main purpose for adopting these control measures is to ensure crystallization temperature as well as stabilization of process parameters, so as to ensure product quality. The withdrawal of strip billet is realized by means of the dragger, and the time of drawing, stop and reverse pushing by the dragger is continuously adjustable. The optimal control parameter should be determined and timely adjusted according to different materials, different specifications and surface quality conditions. The drawing is controlled by PLC program, realizing cyclical actions of drawing, stop, and reverse pushing.
?
Ⅳ. ?Equipment parts list
?
- - - -
No. | Equipment Name | Unit | QTY |
1 | Line frequency induction smelting furnace (including melting groove and lining building material) | set | 1 |
2 | Iron core, water jacket and coil of smelting furnace | set | 1 |
3 | Tundish | set | 1 |
4 | Line frequency induction holding furnace (including melting groove and lining building material) | set | 1 |
5 | Iron core, water jacket and coil of holding furnace | set | 1 |
6 | mould for lining building | set | 1 |
7 | crystallizer | set | 2 |
8 | graphite mould | set | 1 |
9 | Sealing steel mould of crystallizer | set | 1 |
10 | Dummy bar (made of stainless steel) | set | 1 |
11 | Dummy plate | set | 1 |
12 | Cooling water distribution device for crystallizer | set | 1 |
13 | Secondary cooling device | set | 1 |
14 | Withdrawal machine | set | 1 |
15 | Hydraulic follow-up shearing machine | set | 1 |
16 | Coreless coiler | set | 2 |
17 | Water-cooled cable for smelting furnace | set | 1 |
18 | Hydraulic system | Complete set | 1 |
19 | Electrical control system | Complete set | 1 |
20 | Regulating transformer (no-load, stepped) for smelting furnace | set | 1 |
21 | Regulating transformer (no-load, stepped) for holding furnace | set | 1 |
22 | Gas protection device | set | 1 |
23 | Surface temperature thermometer | set | 1 |
24 | Special tools for machine unit | ? | ? |
- - - -
?
Ⅴ.?Date of Delivery:
? ??To be delivered within 75 days after the contract becomes effective.
?
Ⅵ.?After-sales service
? ? 1. The main body of the equipment will have one year of free warranty, and special components shall be discussed separately;
? ? 2. During the trial-production period (within 3 months after equipment commissioning is finished), our company will dispatch a professional technician for follow-up service;
Within the warranty period, if fault occurs due to quality problem, our company will dispatch personnel to the site to solve the problem within 72 hours after receiving the notice;
After the warranty period of the equipment is expired, our company will offer effective solutions within 24 hours after receiving the notice, and will dispatch personnel for maintenance work if the user fails to solve the problem, only charging the cost expenses.
For annual overhaul of equipment, our company will dispatch professional technician to join the users in formulating the turnaround plan, free of charge;
Within the warranty period, our company can dispatch professional technician to the site to check the operation condition of equipment and provide field service.
After the warranty period of equipment expires, one return visit can be made on invitation once per half a year.
? ? 3. If our company has innovation and improvement points or constructive suggestions for similar equipments, we will inform the user in time.
?
?
Wuxi Huadong Industrial Furnace Co.,Ltd
Welcome to visit and inspect!
Contact persone: Angel Zhang
Contact phone:+86-13921168736
Email: wxzhangying@126.com
Wuxi Huadong Industrial Electrical Furnace Co.,Ltd.
Address: Xishan district,Bashi Industrial Park, Wuxi, Jiangsu, China, 214000
Tel: 86-510-83788308
聽 聽 Our company is located at the northeast of Wuxi, Jiangsu Province, with only 2.5 hours of driving distance to Shanghai Pudong International Airport, and the traffic is very convenient.
Wuxi Huadong Industrial Furnace Co., Ltd is a comprehensive enterprise integrating scientific rese